Chemical Plant Painting - Protection and Durability for Your Operation.
Navigate the complexities of maintaining your chemical plant with our expert painting services. We offer specialized coatings and detailed surface preparation to meet rigorous operational demands. Learn how we can safeguard your facility against corrosion, enhance safety, and ensure compliance with regulatory standards.
Navigate the complexities of maintaining your chemical plant with our expert painting services. We offer specialized coatings and detailed surface preparation to meet rigorous operational demands. Learn how we can safeguard your facility against corrosion, enhance safety, and ensure compliance with regulatory standards.
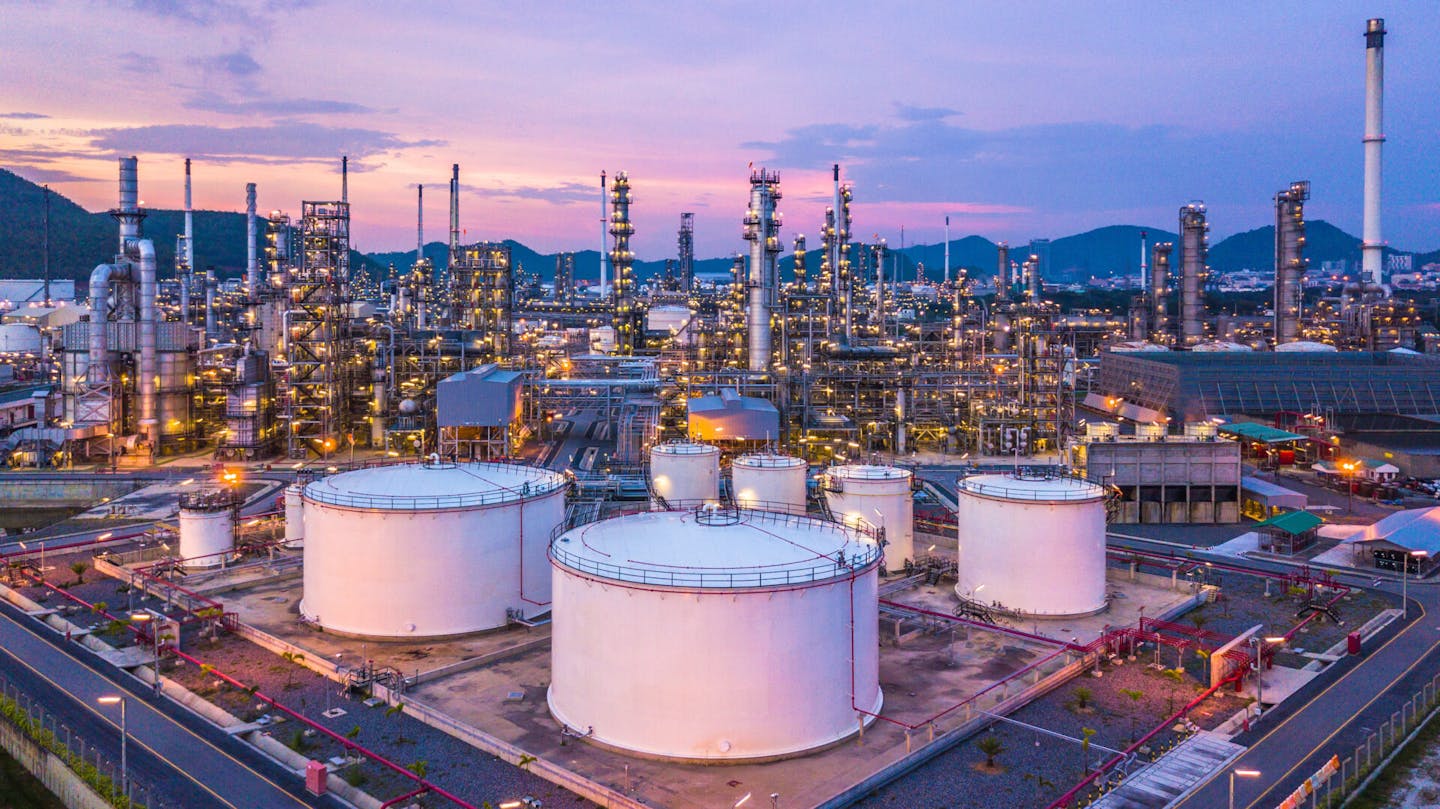
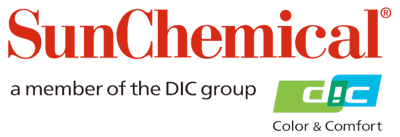
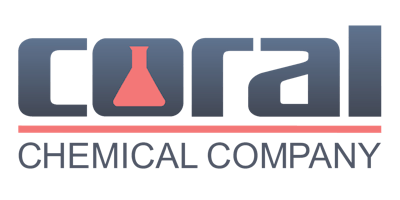

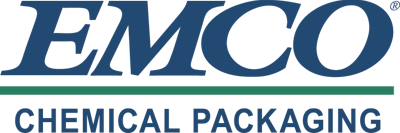
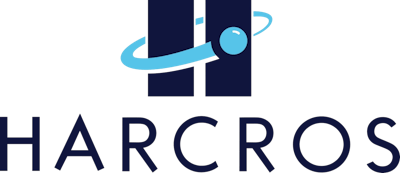
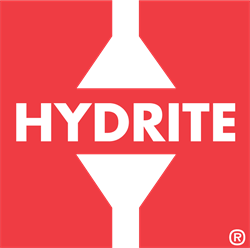
Maintaining the integrity of a chemical plant requires more than just routine upkeep; it demands specialized painting and coating solutions that can withstand the harsh environments and aggressive chemicals inherent to these facilities. With over four decades of experience, our team brings unparalleled expertise in selecting and applying the most durable, resistant, and compliant coatings to protect your infrastructure.
From surface preparation to the final application, we focus on extending the lifespan of your assets, enhancing safety, and ensuring your operations are not just compliant, but also visually appealing and efficient. Let us show you how our tailored painting solutions can contribute to the ongoing success and reliability of your chemical plant operations.
Painters USA is familiar with the most common types of corrosive wear and tear in chemical plants:
- Uniform corrosion usually occurs on unprotected structures and eventually weakens those surfaces and structures.
- Galvanic corrosion results when two or more dissimilar metals are in contact with each other and share a common environment.
- Crevice corrosion occurs when airborne contaminants like chemical salts collect and combine with moisture in areas that are hard to access and difficult to protect.
- Pitting or pit corrosion is insidious, as it’s caused by tiny pinholes and holidays in coating systems that can occur with improper coating products or inferior application.
- Stress corrosion cracking is due to tensile stress, usually caused by operational temperature differences, in combination with a corrosive chemical medium.
Problems You Have That We Can Solve
In environments where chemical exposure is constant, the right protective coatings are crucial to prevent corrosion and extend the lifespan of structures and equipment.
Ensuring your facility adheres to stringent environmental regulations requires specialized coatings that can withstand harsh conditions while maintaining compliance.
Specialized coatings are needed to resist the damaging effects of chemical spills, ensuring the integrity of floors and containment areas.
Facilities require coatings that can withstand extreme heat or offer fire resistance, protecting structures and equipment from damage.
High-traffic areas need coatings that can endure constant wear and tear without degrading, ensuring ongoing operational efficiency.
Coatings must be flexible enough to withstand temperature fluctuations without cracking or peeling, ensuring protection year-round.
Surface prep for any structures and surfaces
Proper industrial cleaning and surface preparation are critical steps in any chemical plant painting or coating project. Painters USA commonly uses pressure washing with detergents and chemicals to neutralize the surface and remove visible and non-visible contaminants
We may recommend abrasive blasting using an appropriate blasting medium for the surface and operating conditions. If abrasive blasting is not practical, we can use manual cleaning methods. While this increases upfront costs due to additional prep time, it saves time and money in the long run by maximizing performance and service life.
Whichever industrial cleaning method we use, once the surface is decontaminated, we address failed areas. Existing coatings are removed to an acceptable condition for adherence and feathered if necessary, which is a technique that creates a gradual transition from a tightly adhered coating to an exposed surface.
Coatings for primary and secondary containment
Painters USA will give special consideration to your primary and secondary containment systems, to keep these critical storage tanks protected from coating breaches or “holidays” (holes or voids, often undetectable without a qualified coating inspection) that could lead to corrosion and leaking.
OSHA, the Environmental Protection Agency, and many industry standards have regulations and requirements for containment systems that store potentially hazardous materials or waste. We will play our part in helping you with all your compliance obligations, and that includes doing our work safely, in accordance with OSHA recommendations and requirements.
Long-lasting, corrosion-resistant coatings
Modern coatings have been formulated to resist corrosion from any sources or operational conditions. Painters USA will choose the right solution for your needs and priorities:
- Coatings for all conditions, from brutal heat to extreme cold, and high humidity to dry climates and heavy sun exposure.
- Superior resistance to abrasion and impact.
- Flexibility to resist structural flex.
- Durable adhesion and bonding for long-lasting performance on any substrate.
- Quick curing for fast project completion and return to service.
Why choose Painters USA?
Maintenance is disruptive. You need a team that gets in and out ASAP. That’s why we pride ourselves with our large, well-trained crews that meet your deadlines and minimize downtime – our speciality!
Being on-budget is as important as being on-time, so we prepare accurate estimates and bids for no unwanted surprises.
We aim to meet or exceed quality expectations, backed by warranties and recommending the best materials to balance performance and costs.
For convenience and single-point-accountability, we have the resources and capacity to work across multiple sites in the US, including remote / rural locations.
Our commitment to safety—backed by ISN RAVS Plus® status and an exemplary TRIR rating—reduces workplace hazards and legal / financial risks in your facilities.
Painters USA is fully licensed and insured, and our crews are full-time employees who have undergone thorough background checks.
We are happy to share client references based on your industry or facility challenges and goals for the greatest relevance to your situation.
As a woman-owned business, we can help you diversify and expand your supplier network.
Enhance Facility Durability and Appearance
Protect your investment and showcase your commitment to excellence. Our durable and aesthetically pleasing coatings are designed to withstand the harsh conditions of chemical plants while maintaining a professional appearance. Let us help you extend the life-and enhance the look-of your facility.
Our happy clients. Both big and small
Minimize Downtime with Efficient Solutions.
Time is money, especially in high-demand chemical production environments. Our quick-curing coatings minimize downtime, allowing for a faster return-to-production without sacrificing quality or safety. Discover how our efficient solutions can support your operational goals.
Time is money, especially in high-demand chemical production environments. Our quick-curing coatings minimize downtime, allowing for a faster return-to-production without sacrificing quality or safety. Discover how our efficient solutions can support your operational goals.
